Platform Deck Cost A Comprehensive Guide
Platform deck cost is a critical factor to consider when planning your outdoor living space. Understanding the various elements that contribute to the overall price is essential for making informed decisions. This guide explores the different facets of platform deck pricing, from material selection to design complexity, to help you estimate the total project cost.
This in-depth analysis covers defining platform deck costs, breaking down the various expenses involved, examining influencing factors, and providing methods for accurate cost estimation. We’ll also compare different materials and designs to aid in your decision-making process.
Cost Breakdown for Platform Decks
Platform decks, a popular addition to homes and recreational areas, offer versatile outdoor spaces. Understanding the detailed cost breakdown is crucial for homeowners and contractors alike to manage budgets effectively. Accurate estimations enable realistic planning and avoid potential financial surprises.
A comprehensive cost analysis considers various factors, including material selection, labor rates, permit requirements, and safety protocols. This detailed breakdown allows for a more informed decision-making process, ensuring the project aligns with financial expectations.
Material Costs
Material costs vary significantly depending on the chosen materials for the platform deck. Different materials offer distinct advantages in terms of durability, aesthetics, and long-term maintenance. Careful consideration of these factors ensures the chosen material aligns with the project’s specific needs and budget.
- Wood: Wood remains a classic choice for platform decks. Pricing depends on the type of wood (e.g., pressure-treated lumber, cedar), its quality, and the quantity required. For example, pressure-treated lumber, while more affordable, may need more frequent maintenance compared to cedar, which can be more expensive upfront but requires less upkeep.
- Composite: Composite decking materials are engineered alternatives to wood, often boasting enhanced durability and resistance to moisture and rot. Composite materials typically have a higher initial cost compared to wood, but long-term maintenance costs are often lower. For instance, a composite deck may require less staining and sealing than a comparable wood deck.
- Concrete: Concrete platforms offer a robust and durable option. The cost of concrete platforms depends on factors like the size of the platform, the complexity of the design, and the cost of labor for pouring and finishing. Concrete is generally more expensive than wood or composite, but its longevity often justifies the higher initial investment.
Labor Costs
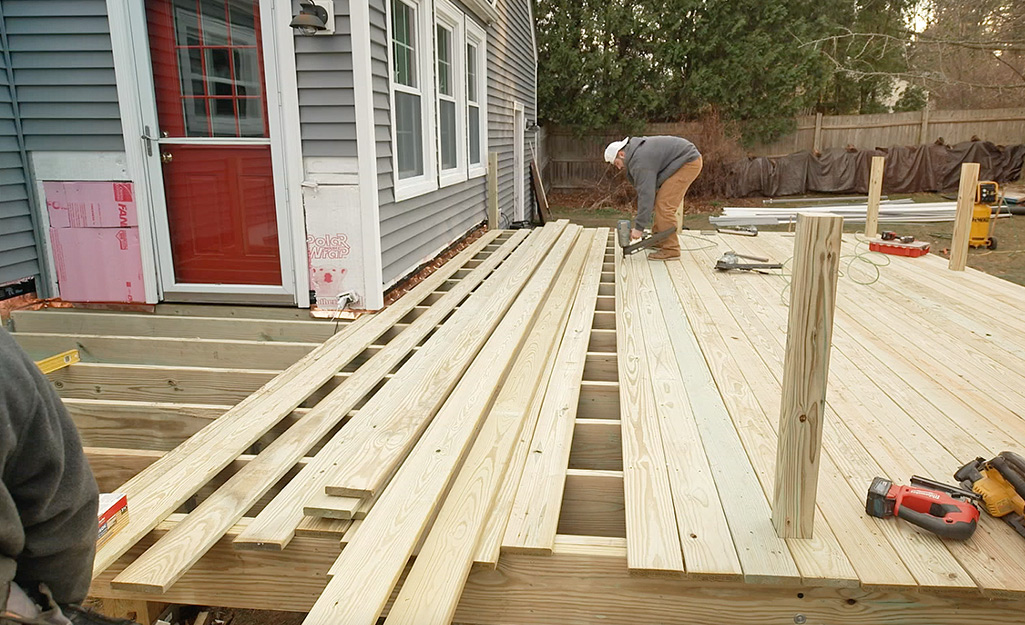
Labor costs are a substantial component of platform deck construction. Factors influencing labor costs include the complexity of the design, the size of the platform, and the local labor market’s rates. Experienced and skilled labor typically commands higher rates.
- Framing and Installation: The cost for framing and installing the deck’s structural components is a major labor expense. The complexity of the framing, including support beams and joists, will directly influence the labor cost. For example, a more intricate platform design with curved or angled support structures will require more labor hours and, consequently, higher costs.
- Finishing and Refinishing: Finishing and refinishing the deck, including sanding, staining, sealing, or painting, accounts for a significant portion of labor costs. The extent of the finishing work will directly affect the labor costs.
- Permitting and Inspections: While not directly related to the construction itself, the costs associated with obtaining necessary permits and inspections are still significant. These costs vary based on local regulations and the complexity of the project. For example, a platform deck with unusual features may require more detailed inspections, increasing the associated permitting costs.
Permitting and Safety Costs
Obtaining permits and conducting inspections are crucial steps in the platform deck construction process. These costs can vary significantly based on local regulations and the project’s specific requirements. Adequate safety measures are also essential to ensure a safe construction site.
- Permits and Inspections: Local building codes often require permits for platform decks, with associated fees varying based on the jurisdiction. Inspections during construction ensure adherence to safety standards and code compliance. The costs of permits and inspections should be factored into the overall project budget.
- Safety Measures: Implementing appropriate safety measures, such as safety harnesses, fall protection, and proper equipment for handling materials, is crucial to protect workers and prevent accidents. These safety measures will be included in the labor costs. For example, a large-scale platform deck project may necessitate specialized safety equipment, increasing the associated costs.
Cost Breakdown Table
Material | Labor | Permits & Inspections | Safety | Other |
---|---|---|---|---|
Wood (Pressure-Treated) | $5,000 – $10,000 | $200 – $500 | $100 – $200 | $300 – $500 |
Composite | $6,000 – $12,000 | $200 – $500 | $150 – $300 | $400 – $600 |
Concrete | $8,000 – $15,000 | $300 – $700 | $200 – $400 | $500 – $800 |
Note: These are estimated costs and can vary significantly based on the project’s specific details. Local material and labor costs will influence the final figures.
Factors Affecting Platform Deck Cost
Platform deck construction involves a range of considerations that significantly impact the final price. Understanding these factors is crucial for project planning and budgeting. From location and design to materials and construction methods, each aspect plays a vital role in determining the overall cost.
Location Impact on Platform Deck Costs
Geographic location substantially influences platform deck costs. Higher labor costs in urban areas, or areas with a high demand for skilled tradespeople, will invariably increase the overall project expense. Additionally, material costs can vary greatly based on local availability and demand. For example, a deck in a region with abundant lumber resources might see lower material costs compared to an area with limited local supply. Furthermore, local building codes and regulations can also impact the required materials and labor hours, adding to the overall cost.
Design Complexity and Platform Deck Costs
The complexity of the platform deck design directly correlates with the project cost. A simple, straightforward design with minimal features will typically be less expensive than a more intricate design with numerous components, specialized features, or unique aesthetics. Elaborate designs often require more specialized materials, intricate fabrication, and extended labor hours. For instance, a deck with multiple levels, custom railings, or elaborate lighting systems will have a higher price tag compared to a basic deck with standard features.
Material Choices and Platform Deck Costs
The selection of materials significantly impacts the cost of a platform deck. Premium materials, like exotic hardwoods or composite decking, usually command higher prices than more common, affordable options. The quality and durability of the materials also play a crucial role. For example, a deck built with pressure-treated lumber will have a lower initial cost but may require more frequent maintenance compared to a deck made of composite materials. The lifespan of the materials is also a critical factor in the long-term cost of ownership.
Construction Method Cost Comparison
Different platform deck construction methods yield varying price points. The choice between prefabricated and custom-built decks has a considerable impact on the overall cost. Prefabricated decks, often assembled from pre-cut components, typically offer lower costs due to streamlined production processes. However, custom-built decks offer greater flexibility in design and customization, but this often comes with higher costs.
Table Comparing Construction Methods
Construction Method | Cost | Flexibility | Time |
---|---|---|---|
Prefabricated | Lower | Limited | Faster |
Custom-Built | Higher | High | Slower |
This table provides a general comparison, and specific costs will vary based on individual project requirements and local market conditions.
Estimating Platform Deck Costs
Source: timbertech.com
Accurately estimating the cost of a platform deck is crucial for project planning and budgeting. A well-executed estimate considers all material and labor expenses, ensuring the project stays within budget and on schedule. This section delves into various methods for estimating platform deck costs, detailing the steps involved and providing practical examples.
Methods for Estimating Platform Deck Costs
Several methods can be employed to estimate platform deck costs, each with its advantages and limitations. A combination of these approaches often yields the most reliable results. Common methods include using material cost databases, consulting with contractors, and performing detailed calculations based on project specifications.
Steps Involved in Creating a Platform Deck Cost Estimate
Creating a precise cost estimate involves a systematic approach. This includes meticulously documenting project specifications, calculating material quantities, and factoring in labor costs and potential contingencies.
Step-by-Step Guide to Estimating Platform Deck Costs
This guide provides a structured approach to estimating platform deck costs, emphasizing the importance of precise measurements and accurate material calculations.
- Define Project Specifications: Clearly define the platform deck’s dimensions (length, width, height), desired materials (wood type, decking material, railing material), and any special features (e.g., stairs, supports). Thorough documentation of these details is essential for accurate costing.
- Measure the Platform Deck Area: Accurately measure the platform deck’s length and width to determine the square footage. For irregular shapes, divide the area into simpler shapes (rectangles, triangles) and calculate the area of each part.
- Calculate Material Quantities: Determine the quantity of each material needed. This includes decking boards, joists, framing materials, and fasteners. Consult material specifications for required quantities per square foot.
- Determine Labor Costs: Research local labor rates for platform deck construction. These rates vary based on experience level and location. Consider labor costs for different tasks, such as framing, decking, and finishing. Include potential costs for permitting and inspections.
- Factor in Material Costs: Obtain pricing information for the chosen materials from local suppliers or online retailers. Compare prices and select the most cost-effective options. Consider factors such as material quality and supplier reliability.
- Calculate Total Costs: Sum up the material costs, labor costs, and any other relevant expenses (e.g., permits, inspections). Factor in potential contingencies (e.g., unforeseen issues or material shortages). This step involves adding up all costs from previous steps.
- Review and Revise: Carefully review the estimate for accuracy. Revise the estimate as needed to account for any changes in specifications or material costs.
Calculating Material Quantities for Different Platform Deck Sizes
Accurate material quantity calculations are vital for accurate cost estimations. These calculations vary depending on the chosen materials and the platform deck’s design.
Platform Deck Size (sq ft) | Decking Boards Required (linear ft) | Joists Required (linear ft) |
---|---|---|
100 | 300 (assuming 3-inch wide boards) | 200 (assuming 2-inch wide joists) |
150 | 450 (assuming 3-inch wide boards) | 300 (assuming 2-inch wide joists) |
200 | 600 (assuming 3-inch wide boards) | 400 (assuming 2-inch wide joists) |
Note: These are example calculations and the exact quantities will depend on the specific design and spacing of the platform deck.
Example of a Platform Deck Cost Estimate
Consider a 100 sq ft platform deck built with pressure-treated lumber for framing and composite decking.
Item | Quantity | Unit Cost | Total Cost |
---|---|---|---|
Pressure-Treated Lumber (Framing) | 100 linear ft | $5/linear ft | $500 |
Composite Decking | 300 linear ft | $8/linear ft | $2400 |
Fasteners | 100 units | $0.50/unit | $50 |
Labor (Installation) | 20 hours | $25/hour | $500 |
Permitting | 1 | $100 | $100 |
Total Estimated Cost | $3550 |
Platform Deck Cost Comparisons
Comparing platform deck costs involves more than just the initial material price. Lifespan and maintenance needs significantly impact the overall cost-effectiveness of different materials and designs. Understanding these factors is crucial for making informed decisions when building a platform deck.
Material Cost Comparisons
Different platform deck materials vary significantly in price. Wood, a classic choice, can range from affordable pressure-treated lumber to more expensive hardwoods. Composite materials, while typically more expensive upfront, often exhibit longer lifespans and lower maintenance requirements. Aluminum, though costly, offers exceptional durability and resistance to weathering. The initial cost difference needs to be weighed against long-term maintenance and replacement costs.
Longevity and Maintenance Costs
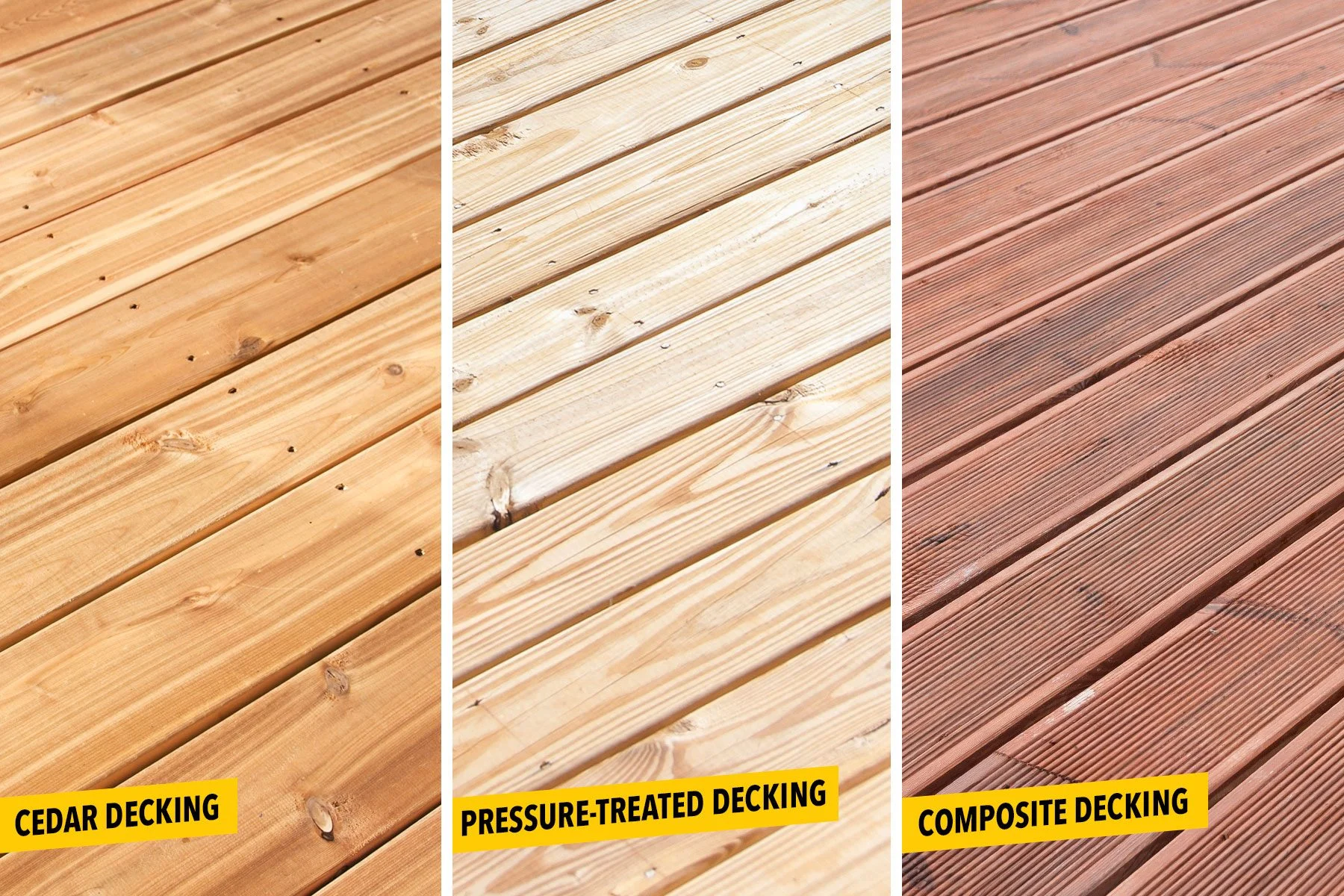
The longevity and maintenance needs of platform deck materials are directly related to their cost-effectiveness. Pressure-treated lumber, for instance, requires periodic sealing and can be susceptible to rot and insect damage, leading to higher maintenance expenses over time. Composite materials, resistant to rot, insects, and moisture, generally require less maintenance, leading to lower long-term costs. Aluminum, with its inherent corrosion resistance, requires minimal maintenance, although the initial cost is higher. Choosing a material that aligns with your budget and desired level of maintenance is essential.
Cost-Effectiveness of Different Designs
Platform deck designs can influence costs significantly. A simple, straightforward design, while potentially less expensive initially, may require more frequent repairs and replacements over time due to its simpler structure. More complex designs, while initially more costly, may offer enhanced functionality and potentially lower long-term maintenance. Factors like the chosen framing method and the complexity of the railing system can also influence the overall cost-effectiveness. Consider the intended use and frequency of use when determining the ideal design.
Cost-Benefit Ratio Analysis, Platform deck cost
The cost-benefit ratio considers the initial cost, lifespan, and maintenance requirements of different materials and designs. A material with a high initial cost but a very long lifespan and low maintenance might have a superior cost-benefit ratio over a less expensive option that requires frequent replacements and repairs. Factors like the local climate, the intended use of the deck, and personal preferences should all be considered.
Platform Deck Material Comparison Table
Material | Initial Cost | Lifespan (Years) | Maintenance Cost (Estimated) |
---|---|---|---|
Pressure-Treated Lumber | Low | 8-15 | Moderate (periodic sealing, repairs) |
Composite Decking | Medium-High | 20-30 | Low (minimal sealing and repairs) |
Aluminum | High | 30+ | Very Low (minimal maintenance) |
Note: Costs and lifespans are estimates and can vary based on specific factors and local conditions.
Platform Deck Cost Considerations
Beyond the initial cost breakdown and influencing factors, several crucial considerations can significantly impact the overall expense of a platform deck project. Careful attention to these areas can prevent unexpected budget overruns and ensure a smooth project execution.
Understanding the interplay between professional advice, regulatory compliance, insurance requirements, and contractor selection is vital for achieving a successful and cost-effective platform deck project. These considerations often involve substantial financial implications and should be addressed proactively.
Importance of Professional Consultations
Professional consultations with engineers or architects are essential in accurately estimating platform deck costs. They can assess site-specific conditions, ensuring the structure meets safety standards and local building codes. A qualified professional can identify potential issues, like soil bearing capacity, that could lead to costly modifications or repairs later on. This proactive approach minimizes the risk of unforeseen expenses and helps create a robust foundation for the project.
Role of Permits and Inspections
Permits and inspections are integral parts of platform deck cost management. Acquiring the necessary permits from local authorities involves fees and timelines that can affect project scheduling and budget. Inspections, conducted by authorized personnel, ensure compliance with building codes and safety regulations. These checks are not just bureaucratic hurdles; they verify the structure’s safety and longevity. Failure to comply with permit and inspection requirements can lead to project delays, fines, or even the need for costly revisions.
Impact of Insurance Considerations
Insurance considerations play a significant role in platform deck costs. Liability insurance protects the owner from potential claims arising from accidents or damages related to the deck. The type and amount of insurance coverage required will depend on the project’s specifics, such as the deck’s size, location, and intended use. Understanding insurance requirements in advance helps in budgeting for these costs. The premiums and deductibles associated with different insurance policies should be factored into the overall project budget.
Factors to Consider When Choosing a Contractor
Selecting a qualified and reputable contractor is crucial for a successful platform deck project. Experience in similar projects is a key factor to evaluate. Contractor portfolios and references should be reviewed to assess their ability to handle the specific requirements of the project. A strong track record of on-time and on-budget project completion is a positive indicator. Additionally, the contractor’s understanding of local building codes and safety regulations should be carefully examined. The contractor’s reputation and communication style are essential for a smooth and collaborative project.
Typical Costs Involved in Securing Permits and Inspections
The cost of securing permits and inspections varies based on local regulations and the specifics of the project. These costs can include application fees, plan review fees, and inspection fees. Permitting procedures can vary considerably between jurisdictions, and some may require additional inspections depending on the complexity of the structure. For example, a simple deck might only require a building permit, while a more elaborate structure could necessitate inspections from multiple departments, such as structural engineering, fire safety, and electrical code. It is essential to research the specific permitting requirements in the relevant jurisdiction. Detailed cost breakdowns can be obtained from local building departments.
Variations in Platform Deck Costs
Platform deck construction costs are influenced by a multitude of factors, making precise estimations challenging. Understanding these variations is crucial for homeowners and contractors alike to manage expectations and project budgets effectively. Geographical location, building codes, design complexity, size, and material availability all play a significant role in shaping the final cost.
The cost of a platform deck can differ considerably depending on the specific location. Factors like labor rates, material prices, and local regulations directly affect the overall project budget. This variance is further complicated by variations in building codes, design choices, and material availability.
Influence of Geographical Location
Geographic location significantly impacts platform deck costs. Higher labor rates in urban areas or coastal regions often translate to increased costs. Material costs can also vary due to transportation expenses and availability. For instance, the price of pressure-treated lumber might be higher in regions with limited local sources. Similarly, specialized or exotic materials used in a unique design might be more expensive in locations with limited availability.
Impact of Regional Building Codes
Regional building codes play a crucial role in determining the permissible design and construction of platform decks. Codes dictate minimum safety standards, required materials, and structural requirements. More stringent codes in certain areas necessitate the use of higher quality materials or more complex design solutions, consequently driving up the cost. For example, a deck in a high-wind zone might require stronger framing and more substantial materials than a deck in a low-wind zone, directly affecting the cost.
Cost Variations Based on Design Complexity
The complexity of the platform deck design directly correlates with the overall cost. A simple, straightforward deck with basic features will generally cost less than a complex deck featuring intricate details, custom railings, or multiple levels. The number of design elements, the level of customization, and the inclusion of advanced features like built-in seating or a pergola significantly influence the final cost. Consider a deck with a built-in grill and a retractable awning; this design complexity will add significantly to the overall cost.
Cost Variations Based on Platform Deck Size
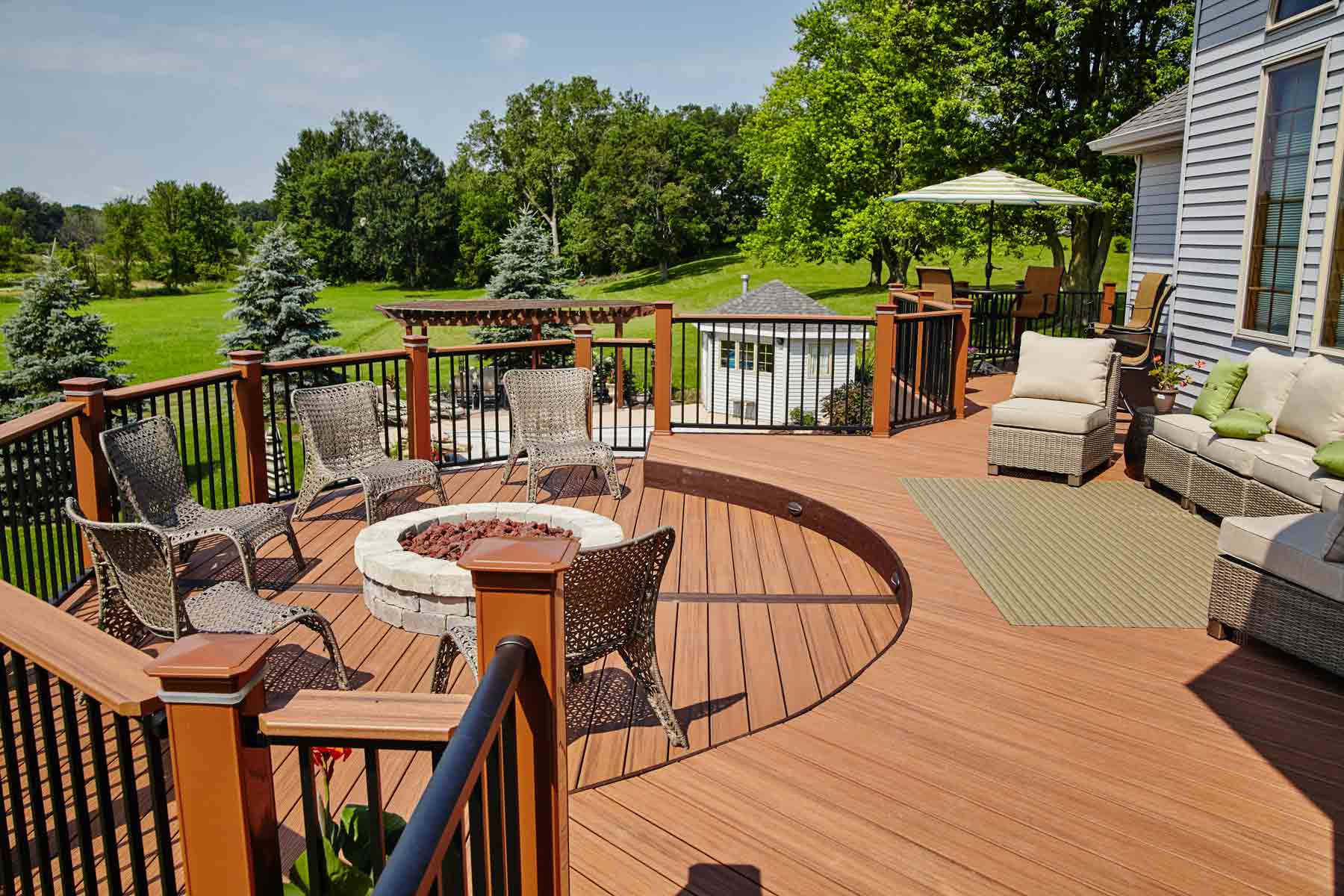
The size of the platform deck directly impacts the material and labor requirements. A larger deck will require more lumber, more fasteners, and more labor hours, resulting in a higher cost. Estimating the material quantities accurately and accounting for waste is essential to avoid cost overruns. For instance, a 10×20 deck will use significantly more materials than a 6×10 deck. This difference in size translates directly to the cost of the project.
Adjusting Cost Estimates Based on Local Factors
Adjusting cost estimates for local material availability and labor rates is essential for accurate budgeting. If a particular material is scarce or expensive in a region, the cost of the project will increase. Similarly, variations in local labor rates will impact the overall cost. It is wise to consult with local contractors and suppliers to obtain accurate pricing for materials and labor. Consider factors like local regulations, permits, and inspections as well, which will have a direct impact on your final cost estimate.
End of Discussion
In conclusion, determining the platform deck cost requires careful consideration of numerous factors. By understanding the components of the cost breakdown, the influence of design choices, and the importance of professional consultation, you can create a realistic budget and make informed decisions. Remember to thoroughly research local regulations, materials, and labor rates for an accurate final estimate.