Cost of Platform Deck A Comprehensive Guide
The cost of platform deck construction can vary significantly depending on several factors. This guide explores the diverse elements impacting the final price, from material choices to labor costs, location specifics, and project complexity.
We’ll delve into the different types of platform decks, examining their associated costs. Tables will illustrate material comparisons and cost breakdowns, offering a clear picture of the expenses involved. We’ll also cover cost estimation methods, savings strategies, and how location affects the final price.
Defining Platform Deck Costs: Cost Of Platform Deck
Source: remodelingcalculator.org
A platform deck, a versatile outdoor living space, is more than just a simple addition to a home. It requires careful consideration of various components, materials, and factors that significantly impact the overall cost. Understanding these elements is crucial for homeowners planning a platform deck project.
Platform decks offer diverse functionalities, ranging from simple relaxation areas to elaborate entertaining spaces. The complexity and features desired will directly influence the budget, and choosing the right material is a key aspect of cost management. Accurately assessing the total project cost requires a detailed understanding of the different components and the factors affecting each.
Platform Deck Components
Platform decks are composed of several essential parts. These include the deck itself, comprising the deck boards, the framing, and the supporting structure. Additionally, railings, stairs, and other features, such as lighting or built-in seating, contribute to the overall cost. The complexity of the design, the desired aesthetics, and the level of customization will directly influence the total cost. A simple platform deck will generally be more affordable than one featuring elaborate features or custom designs.
Platform Deck Types and Associated Costs
Different types of platform decks serve various purposes. A simple, open-air platform deck, suitable for casual relaxation, will likely have a lower cost compared to a covered platform deck with built-in features. Consideration of the desired level of privacy, entertaining space, and the required level of weather protection will influence the final price. For example, a platform deck with a pergola or awning will increase the cost significantly compared to a basic platform.
Factors Influencing Platform Deck Costs
Several factors influence the cost of a platform deck. These include the size and complexity of the design, the chosen materials, the labor costs, and any permits or inspections required. The size of the deck is a primary determinant, with larger decks generally having a higher cost. The complexity of the design, such as intricate railings or custom features, also contributes significantly to the total price. Finally, the chosen materials and their quality directly affect the overall cost. For instance, high-end lumber or composite decking will result in a higher price than more basic options.
Cost Comparison of Platform Deck Materials
Material | Estimated Cost/sq ft | Pros | Cons |
---|---|---|---|
Wood | $8-$25 | Natural beauty, various styles, and relatively easy to work with. | Requires regular maintenance (staining, sealing), susceptible to rot and decay, higher cost of replacement if damaged. |
Metal | $15-$35 | Durable, low maintenance, resistant to rot and insects, long lifespan. | Can be less aesthetically pleasing than wood or composite, higher initial cost, may require specialized installation. |
Composite | $15-$30 | Low maintenance, resistant to rot, insects, and fading, long lifespan. | Higher initial cost compared to wood, may not offer the same aesthetic variety as wood. |
The table above provides a general cost estimate per square foot for different materials. Actual costs will vary depending on local material prices, the specific type of material chosen, and the contractor’s fees. Furthermore, the labor costs for installation should also be factored into the overall budget.
Cost Breakdown
A crucial aspect of platform deck construction is understanding the detailed cost breakdown. This section delves into the various components contributing to the overall expense, from materials to labor and permits. Careful consideration of these factors allows for realistic budgeting and informed decision-making.
Material Costs
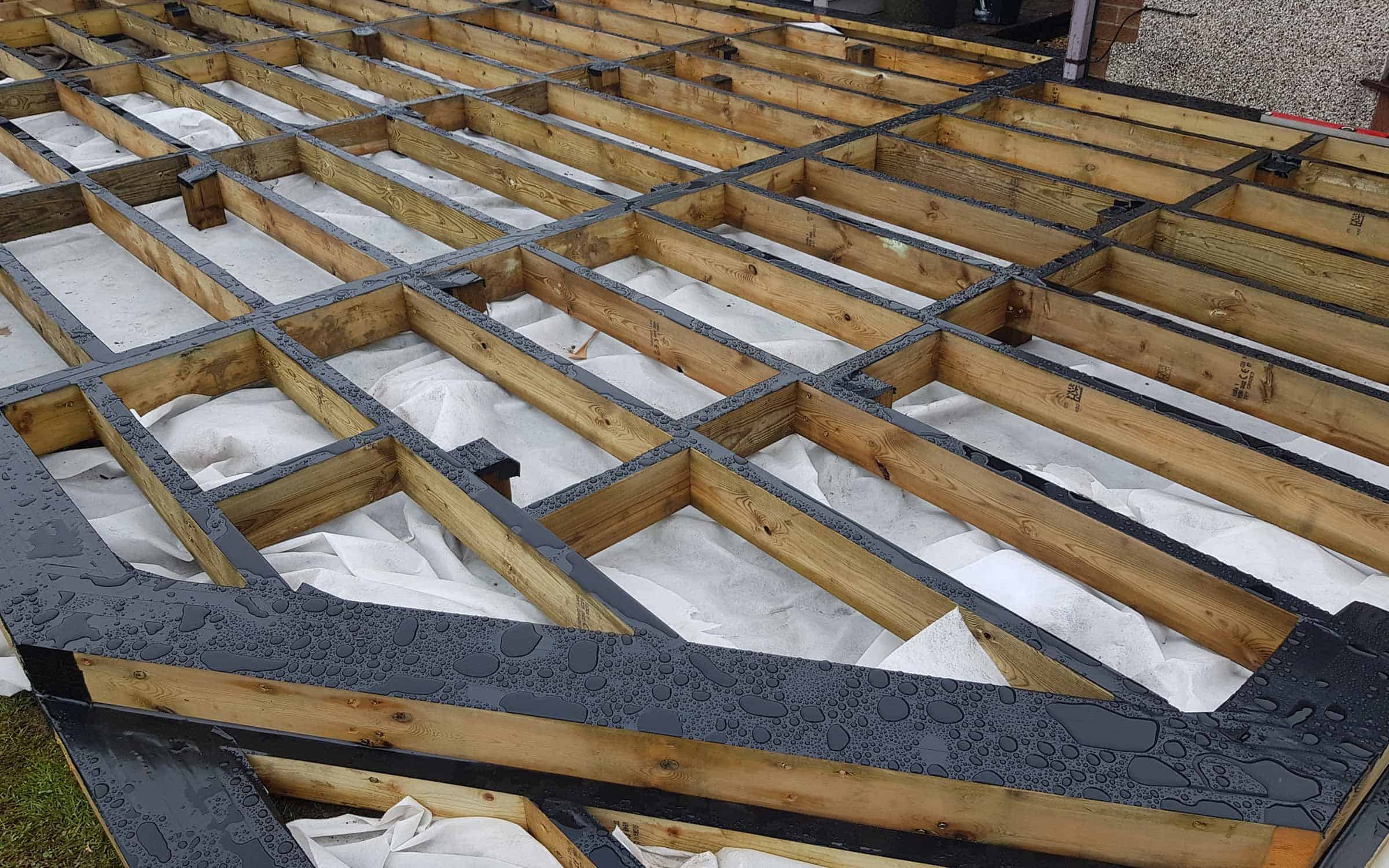
Material costs represent a significant portion of the total platform deck budget. Different types of wood, lumber, and fasteners impact the final price. Factors like the desired size, complexity, and durability of the deck will affect the quantity and quality of materials needed. For instance, pressure-treated lumber, while more expensive upfront, often proves more cost-effective in the long run due to its enhanced resistance to decay and rot. Similarly, high-quality fasteners ensure a sturdy and long-lasting structure, although they will also command a higher price. The choice of materials directly correlates with the overall cost and the lifespan of the deck.
Labor Costs
Labor costs vary based on several factors, including the complexity of the design, the required construction techniques, and the location. For instance, a simple platform deck with a straightforward design will generally involve fewer labor hours than a more intricate or oversized structure. Experienced and licensed contractors command higher hourly rates. Additionally, local labor market conditions and demand influence pricing. The level of expertise required for specific tasks, like framing, decking, and finishing, significantly impacts the overall labor cost.
Permit Costs
Securing necessary permits is a crucial but often overlooked aspect of platform deck construction. These costs vary depending on local building codes and regulations. Local municipalities often have specific guidelines for deck construction, including size restrictions, setbacks, and required inspections. The complexity of the project and the specific requirements of the jurisdiction will dictate the exact cost of permits. Failing to obtain required permits could lead to significant penalties and even construction delays.
Other Expenses
Other costs, while potentially less significant than materials and labor, can still accumulate. These include site preparation, such as leveling the ground or removing existing vegetation, which might involve additional charges. Insurance during construction and potential unforeseen issues, like weather delays, should also be accounted for in the budget. These additional expenses are essential to include in the overall cost estimate for platform deck construction.
Cost Breakdown Table
Category | Description | Estimated Cost (USD) |
---|---|---|
Materials | Wood, lumber, fasteners, decking, and railing | $2,000 – $5,000 |
Labor | Construction, installation, finishing | $3,000 – $8,000 |
Permits | Building, zoning, and inspections | $100 – $500 |
Site Preparation | Leveling, excavation, and debris removal | $500 – $1,500 |
Contingency | Unforeseen issues, material variations | $500 – $1,000 |
Factors Affecting Platform Deck Cost
A platform deck, while offering a versatile and functional outdoor space, is not a one-size-fits-all project. Several key elements significantly impact the overall cost, ranging from site conditions to design complexity and desired customizations. Understanding these factors is crucial for homeowners to accurately budget for their platform deck project.
The cost of a platform deck is influenced by a multitude of factors, some readily apparent, while others may be less obvious but equally important. This section delves into these influencing factors, highlighting their impact on the final project cost.
Site Conditions and Their Cost Implications
Site conditions play a pivotal role in determining the overall cost of a platform deck. Different terrains and existing structures require varying degrees of preparation, which directly affect the project’s budget.
- Uneven Ground: Uneven ground necessitates extensive site preparation, including leveling and potentially the installation of retaining walls. These procedures can substantially increase labor costs and material expenses, often exceeding the cost for projects on level ground. For instance, a project requiring significant excavation and fill may double or even triple the cost of a project on a flat site.
- Existing Utilities: The presence of existing utilities, such as pipes, electrical lines, or drainage systems, beneath the proposed platform deck location often necessitates careful planning and potentially costly adjustments. This may involve rerouting or trenching, impacting both labor and material costs. For example, a project that requires extensive trenching to avoid damaging utilities might add $5,000-$10,000 to the total cost.
- Drainage Considerations: Adequate drainage is critical for preventing water damage and ensuring the longevity of the platform deck. Poor drainage conditions might necessitate the installation of French drains, additional grading, or other drainage systems. These additions increase the cost by adding to labor and material costs.
Design Complexity and Customization Impact, Cost of the platform deck
The complexity of the platform deck design significantly influences its cost. More intricate designs, including multiple levels, unique architectural features, or complex support structures, require specialized expertise and often involve higher material costs. Similarly, customizations play a crucial role in shaping the final price tag.
- Design Complexity: A simple, rectangular platform deck with standard support beams is far less expensive than a multi-level deck with intricate railings, curved edges, or decorative elements. Design complexity increases labor time, potentially requiring more specialized contractors and skilled labor, thereby increasing the cost.
- Customization Options: Custom railing designs, built-in seating areas, or integrated lighting systems add to the overall project cost. Each customization necessitates additional labor, materials, and design considerations, directly impacting the final price.
Comparison of Different Site Conditions
Site Condition | Cost Implications |
---|---|
Level Ground | Lower cost due to minimal site preparation requirements. |
Sloped Ground | Higher cost due to extensive site preparation, potentially including retaining walls and grading. |
Ground with Existing Utilities | Higher cost due to rerouting or trenching needs. |
Cost Estimation Methods
Accurately estimating the cost of a platform deck project is crucial for successful project planning and budget management. Inaccurate estimations can lead to project delays, cost overruns, and even project failure. Robust cost estimation methods, combined with careful consideration of various factors, are essential for achieving desired outcomes.
Estimating platform deck costs requires a multi-faceted approach, considering not only the direct materials and labor but also indirect expenses, potential risks, and contingencies. Several methodologies exist, each with its strengths and weaknesses. Choosing the appropriate method depends on the complexity of the project, available data, and desired level of accuracy.
Methods for Estimating Platform Deck Costs
Various methods are employed to estimate platform deck costs. These methods often involve combining qualitative assessments with quantitative data. A crucial aspect is understanding the specific project context to determine the best approach.
- Analogous Estimation: This method leverages historical data from similar projects to estimate costs for a new project. It’s particularly useful for projects with known similarities to past projects, allowing for quick initial estimates. For example, if a company has built several similar platform decks in the past, historical data on materials, labor, and other expenses can be used to estimate costs for a new project. However, the accuracy of this method relies heavily on the similarity between the projects. Substantial differences can lead to inaccurate estimations. Careful consideration of project specifics is essential.
- Parametric Estimation: This method uses mathematical formulas or algorithms to estimate costs based on quantifiable characteristics of the project, such as the area of the deck or the type of materials used. For instance, the cost per square meter of decking material can be used to estimate the cost of the decking portion of the project. This method provides a more precise estimation compared to analogous estimation, especially when dealing with projects involving standard construction practices. It is important to ensure the chosen parameters accurately represent the project’s scope.
- Bottom-up Estimation: This method involves breaking down the project into smaller components, estimating the cost of each component individually, and then summing these individual costs to arrive at the total cost. This approach provides a granular breakdown of costs, making it useful for complex projects. For example, individual costs for materials, labor, permits, and equipment rental are estimated separately and then added up to determine the total cost of the platform deck project. This method is particularly suitable for projects with unique features or specialized requirements. Care must be taken to avoid overlooking any critical components.
Online Tools and Resources for Cost Estimation
Several online tools and resources can assist in cost estimation for platform deck projects. These tools can automate calculations and provide insights based on industry benchmarks. Leveraging these resources can save time and enhance accuracy.
- Construction Cost Estimators: Numerous online tools are specifically designed to estimate construction costs. These often incorporate data on materials, labor rates, and local regulations. These resources allow for a preliminary cost assessment before engaging in more in-depth analysis. Using these tools can streamline the initial estimation process.
- Industry Benchmarks: Industry publications and websites often provide cost benchmarks for various construction projects. These benchmarks offer insights into average costs for specific materials, labor, and other expenses. Comparing project estimations against industry benchmarks provides a crucial external validation step. This process can be instrumental in identifying potential cost discrepancies.
- Material Pricing Websites: Online platforms offer real-time pricing for construction materials. Using these websites, users can get up-to-date pricing for wood, concrete, and other materials. These tools can be particularly valuable in fluctuating material markets, helping project managers stay abreast of current prices.
Project Management Software for Cost Tracking
Project management software plays a critical role in cost tracking throughout the project lifecycle. These tools can streamline the process of monitoring costs and identifying potential deviations.
- Cost Tracking Capabilities: Software platforms offer features for tracking actual costs against the estimated costs. This allows for proactive identification of potential cost overruns or underspending. Utilizing these features can help project managers maintain control over project budgets.
- Detailed Cost Breakdown: Project management software often provides detailed breakdowns of project costs. This detailed view enables project managers to identify cost drivers and make necessary adjustments. These features can help pinpoint specific areas of potential cost increases or decreases.
- Reporting and Analysis: Project management software generates reports on cost performance. These reports can be instrumental in identifying trends and making informed decisions regarding cost management. Analysis of these reports can highlight areas needing attention or adjustments.
Consulting with Professionals for Accurate Cost Estimations
Engaging with professionals with expertise in platform deck construction is highly recommended for accurate cost estimations. Their insights can be invaluable in identifying potential risks and mitigating potential cost overruns.
- Expert Knowledge: Professionals possess in-depth knowledge of local regulations, material costs, and labor rates. This expertise can lead to a more accurate estimation compared to estimations made by non-professionals.
- Risk Assessment: Experts can identify potential risks and develop mitigation strategies to avoid unexpected costs. Risk assessment is crucial in accurately determining potential future expenses and helps in the overall cost estimation process.
- Contingency Planning: Professionals can advise on the need for contingency planning, which is critical in addressing unforeseen circumstances and budget fluctuations. This crucial element can safeguard against project delays or cost overruns.
Cost Savings Strategies
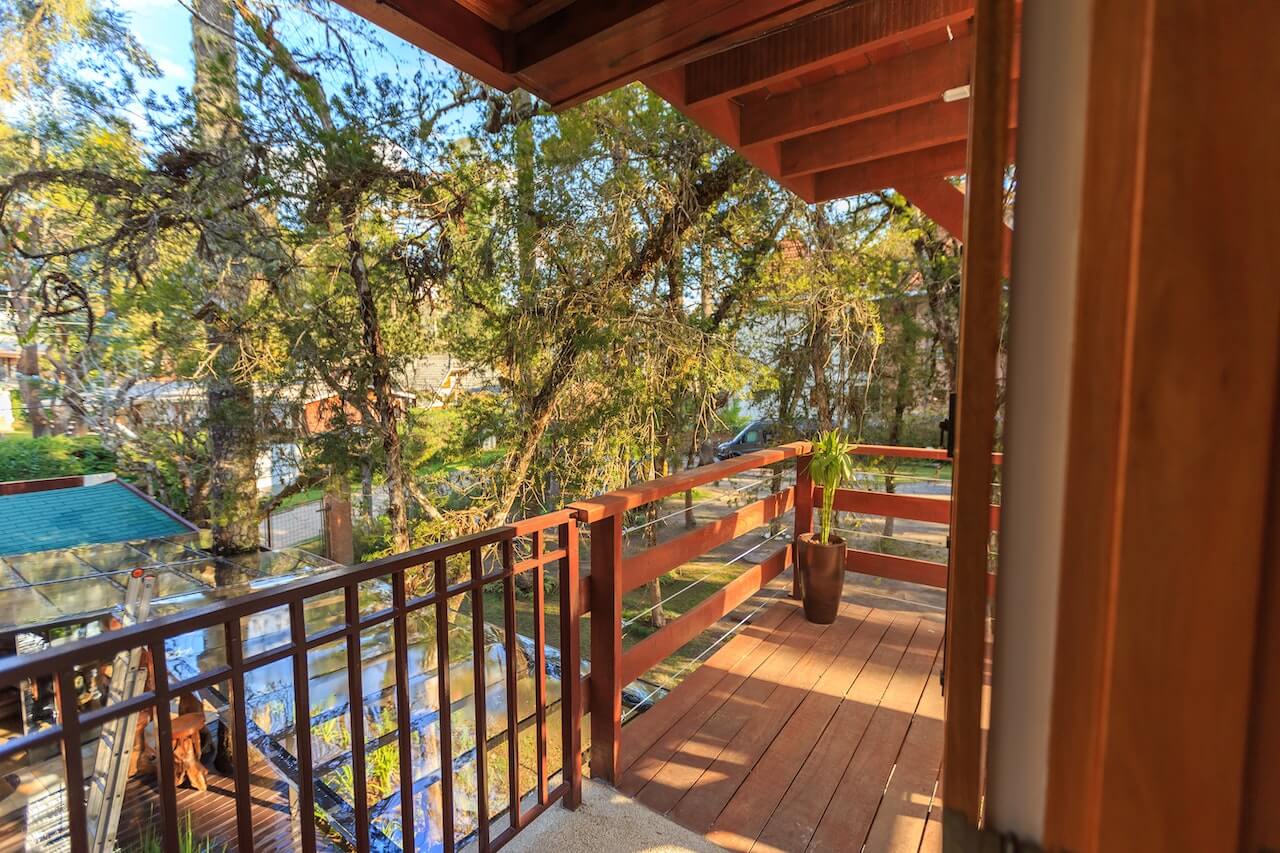
Reducing the cost of a platform deck project without sacrificing quality requires a strategic approach. Careful planning, informed material choices, and resourceful execution are key to minimizing expenses while maintaining the desired aesthetic and functionality. This section details various strategies to achieve this balance.
Strategies for Reducing Platform Deck Costs
Minimizing platform deck costs necessitates a proactive approach to budgeting and material selection. Implementing these strategies can significantly impact the overall project expense.
- Optimizing Design for Efficiency: A well-designed platform deck layout can directly impact the material required and the labor hours needed for construction. Consider the project’s specific needs, including load capacity, aesthetic preferences, and site conditions. A simple, streamlined design can often reduce material use without compromising the project’s overall effectiveness.
- Employing DIY Methods: Certain aspects of a platform deck project can be effectively completed by the homeowner, reducing labor costs. Tasks like basic framing, minor carpentry, and staining can be undertaken by the owner, while professionals are engaged for more complex or specialized work. This method can deliver significant cost savings, especially when combined with careful planning and preparation.
- Exploring Different Material Sources: Materials for platform decks are available from various vendors. Comparing prices and quality across multiple suppliers can lead to substantial savings. Online retailers, local lumberyards, and specialized suppliers often provide competitive pricing. Carefully evaluating the vendor’s reputation and delivery timelines is essential for a smooth project.
- Comparative Material Analysis: Various materials offer different levels of cost and durability. A thorough comparison can guide informed material choices. For example, pressure-treated lumber might be more affordable than composite decking, but composite decking offers a longer lifespan and reduced maintenance needs. Consider the project’s specific needs and budget to make an informed decision.
- Negotiating with Contractors: When employing contractors, transparent communication and negotiation can be beneficial. Clarifying expectations, outlining scope of work, and comparing quotes from multiple contractors are vital for securing a fair and competitive price. Building a strong relationship with the contractor is essential for the project’s smooth progression.
DIY Methods for Cost Reduction
DIY methods offer a practical approach to minimizing platform deck project costs. Certain tasks, if executed correctly, can significantly reduce the overall expenses without compromising the final product’s quality.
- Framing and Assembling Components: Basic framing and assembling components like joists, beams, and supports can be performed by the homeowner. This reduces the labor costs associated with these tasks. Following detailed instructions and safety precautions is crucial for successful execution.
- Installing Railings and Handrails: Simple railings and handrails can be constructed using readily available materials. Following blueprints and adhering to local building codes are important for ensuring structural integrity and safety. DIY installation is suitable for relatively straightforward designs.
- Staining and Finishing: Staining and finishing the platform deck is a task that can often be handled by the homeowner. Using high-quality stain and appropriate application techniques is key to achieving a professional-looking finish. Proper preparation of the wood surface before staining is crucial for a long-lasting result.
Material Cost Comparison
A comparison of material costs is vital for cost-effective decision-making. Various factors, such as material type, quality, and quantity, influence the price.
Material | Approximate Cost (per square foot) | Advantages | Disadvantages |
---|---|---|---|
Pressure-treated lumber | $3-$8 | Affordable, readily available | Requires regular maintenance, shorter lifespan |
Composite decking | $10-$20 | Low maintenance, longer lifespan | Higher initial cost |
Cedar decking | $8-$15 | Natural beauty, relatively low maintenance | Higher cost than pressure-treated, susceptible to rot and insect damage |
Note: Prices are estimates and may vary based on location, vendor, and material quality.
Platform Deck Cost Variations by Location
Platform deck construction costs are significantly influenced by geographic location. Factors like material availability, labor rates, and local regulations all play a crucial role in determining the final price. Understanding these variations is vital for accurate cost estimations and informed decision-making.
Geographic location significantly impacts the cost of platform deck construction. This is due to fluctuations in the cost of materials, labor, and local regulations.
Material Cost Variations
Material costs for platform decks fluctuate considerably based on location. For example, lumber prices vary significantly across different regions. Proximity to lumber mills or timber reserves directly affects the cost of wood, a common material for platform decks. Similarly, the price of composite decking materials, such as PVC or wood-plastic composites, can differ based on manufacturing facilities and transportation routes. The availability of specific types of stone or concrete for retaining walls or other structural elements also impacts pricing. In regions with readily available local resources, materials tend to be more affordable. Conversely, regions reliant on imported materials often face higher costs.
Labor Rate Differences
Labor costs vary significantly depending on the region. Highly populated urban areas often have higher wages for construction workers. Conversely, rural areas generally exhibit lower labor rates. The availability of skilled labor, such as carpenters or deck installers, also influences costs. In areas with a shortage of qualified labor, the cost to hire specialized personnel can be higher. Construction worker experience and certifications can also add to labor costs.
Local Regulations and Building Codes
Local building codes and regulations play a critical role in platform deck construction costs. Different regions have varying regulations concerning deck size, safety features, and building permits. Compliance with these regulations often necessitates additional materials or labor costs. For instance, areas with stringent building codes for earthquake resistance might require more substantial framing and support structures, which, in turn, elevate the project’s overall cost. The complexity of permit acquisition processes and inspection fees can also contribute to cost variations.
Urban vs. Rural Cost Differences
Urban areas typically experience higher platform deck construction costs compared to rural areas. Higher labor rates, stricter regulations, and limited material availability often contribute to increased costs in urban environments. In contrast, rural locations frequently feature lower material costs and labor rates. However, transportation costs to remote locations can offset some of these savings. Furthermore, the availability of local materials and skilled labor may also influence the cost differential.
Regional Material Availability
Regional variations in material availability significantly impact platform deck costs. Regions with abundant local resources for deck materials, such as timber or stone, generally have lower material costs. Conversely, regions reliant on imported materials often face higher costs due to transportation and import duties. The availability of specific materials, such as pressure-treated lumber or specific types of decking, influences pricing.
Illustrative Platform Deck Cost Scenarios
Understanding the cost of a platform deck hinges on its specific design and features. This section provides illustrative examples to help visualize the price range for various projects. Factors such as size, materials, and desired features will significantly impact the overall cost.
Simple Platform Deck Project
A basic platform deck, typically used for casual outdoor seating or a small workspace, can be a cost-effective solution. A 10×12-foot deck constructed of pressure-treated lumber, with a simple railing and basic support structure, will generally fall within a specific price range. Consider the following scenario:
- Dimensions: 10 feet by 12 feet
- Material: Pressure-treated lumber
- Features: Basic railing, simple support beams
- Estimated Cost: $3,000 – $5,000
This estimate assumes standard labor costs in a typical location and accounts for materials and construction. Additional costs may arise if special permits are required or if customized features are added.
Advanced Platform Deck Project
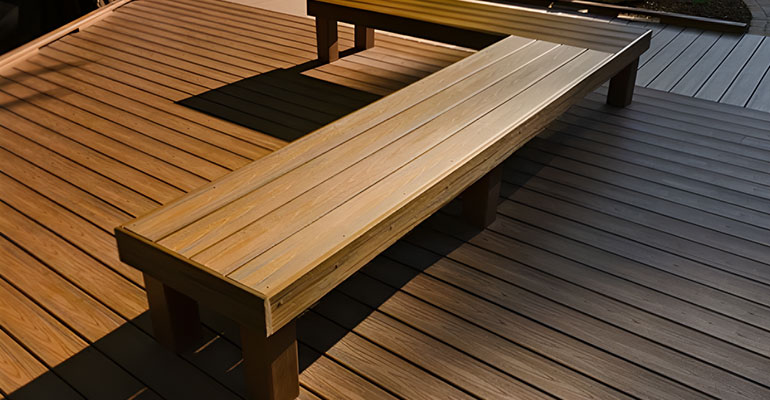
An advanced platform deck can incorporate sophisticated features, leading to a higher cost. This design might include composite decking, elaborate railings, built-in seating areas, or a more complex support structure. Consider the following example:
- Dimensions: 15 feet by 20 feet
- Material: Composite decking, stainless steel railing
- Features: Built-in seating area, integrated lighting, custom pergola
- Estimated Cost: $10,000 – $20,000
The elevated materials and intricate features substantially increase the project’s cost. This type of deck is often tailored to meet specific homeowner needs and preferences. Furthermore, skilled labor and specialized equipment may be required.
Comparison of Small and Large Platform Decks
A comparative analysis of platform deck costs highlights the influence of size and features. The following table illustrates estimated costs for different deck sizes:
Deck Size (sq ft) | Material | Estimated Cost | Features |
---|---|---|---|
100 | Pressure-treated lumber | $4,000 – $6,000 | Basic railing, simple support |
300 | Composite decking | $15,000 – $25,000 | Elaborate railing, built-in seating, pergola |
The larger deck incorporates more elaborate features and premium materials, resulting in a significantly higher cost. Variations in location, labor rates, and material costs can further influence the final price. It is crucial to account for these factors during the cost estimation process.
Final Conclusion
In conclusion, understanding the cost of a platform deck requires a comprehensive approach. By considering materials, labor, permits, and location-specific factors, you can make informed decisions. This guide provides a roadmap to estimate costs accurately, explore savings options, and ultimately, build your dream platform deck within budget. Remember to consult professionals for personalized advice and precise estimates for your specific project.